WATERJET CUTTING SYSTEMS FOR THE FUTURE
A brand new generation of Waterjet Systems has been presented together with the Austrian Partner STM, leader in his field with more than 20 years of experience, to meet the specific needs of the clients and their special cutting applications.
A modern concept and efficient design characterize a reliable system that fulfils the latest shape cutting requirements.
Actech offers flexible, high-performance and tailor-made cutting solutions for any material and desired shape.
The Waterjet Systems Ecocut, Standard and Premium find their daily, efficient application in cutting various materials up to a thickness of 100mm, including:
- industrial gaskets, plastic materials, rubber
- foam materials
- stainless steel, aluminum, copper, titanium
- carbon fiber reinforced plastic, carbon fiber, composite materials
- granite, marble, glass, ceramics
The key benefits are that these waterjets cut do NOT cause any thermal stress and do NOT set free any toxic dust and/or vapor. The only tool we are using is pure water or – in abrasive mode – water and garnet sand. That’s it!
The specially designed EasyCut waterjet cutting program uses CAD shapes for “wysiwyg” (what you see is what you get) programming and guarantees user-friendly handling and high-quality cutting performance. Reliable components and modern engineering minimize maintenance and costs for spare parts.
These Waterjet System are ideally suited for short-run part production, just-in-time manufacturing, bulk production, prototyping and product development. They do not require tool changes or complex fixturing and allow you to reduce setup times by up to 50%.
Markets:
technical textiles/material and composites.
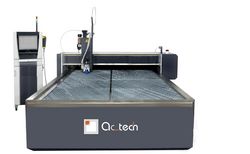 |
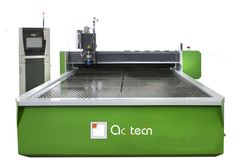 |
|
Ecocut, Standard and Premium Waterjet Systems are a 3-axis CNC-controlled bridge-type machines with rack and pinion drive on both sides. Specially designed, dust- and dirt-protected slideways ensure abrasive resistance. The entire systems are made of high-quality stainless steel and aluminum. Brushless digital AC servo motors guarantee precise, low-vibration positioning of the cutting head. All systems, with single and multiple cutting heads, allow you to adjust the z-axis directly at the simple push of a key. The systems are extremely robust and have been designed for continuous operation.
Dimensions:
WS 1 0 1 0 cutting area 1000 mm x 1000 mm
WS 1 5 1 5 cutting area 1500 mm x 1500 mm
WS 2 5 1 5 cutting area 2500 mm x 1500 mm
WS 3 0 1 5 cutting area 3000 mm x 1500 mm
WS 3 0 2 0 cutting area 3000 mm x 2000 mm
WS 4 0 2 0 cutting area 4000 mm x 2000 mm
In addition, waterjet cutting systems with a length of up to 12m are available
|
|
Control unit and CNC controller
Fitted with an MS Windows standard PC, a fully digital CNC controller, digital CNC axes, as well as digital AC servo motors, the systems ensure precise background control of safety management, axis positioning and SPS input/output management.
The benefits are plain-text malfunction management, a high-speed CNC controller for low-vibration axis positioning, as well as a 10/100/1000 MBitnetwork connection for easy data management.
EasyCut waterjet cutting program
You can easily create and efficiently place the cutting program. The DXF and HPGL import function allows for an easy data import from any CAD program. Efficient and cost-saving placing of the cutting files minimizes your waste. In addition, our clients have the possibility to extend material lists as well as to switch over to the US measuring system.
The cutting sequence and direction, as well as pressure and abrasive settings can be easily changed and adjusted via the EasyCut software.
|
|
Abrasive dosing unit
The abrasive hose from the mini hopper to the abrasive head is very short and ensures constant abrasive flow. This accelerates cutting by up to 20% and increases cutting quality. The abrasive medium container has a capacity of 250kg of abrasive.
You can refill the container at any time and place it up to 10 meters away from the mini hopper.
The abrasive pressure hopper is located directly under the abrasive medium container and automatically feeds the mini hopper at the z-axis with abrasive. Through precise dosing, the abrasive hopper system guarantees reliability and optimum cutting performance as well as savings in abrasive use.
|
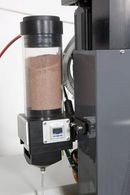 |
Automatic height and collision sensor
The height sensor automatically controls the distance between the cutting head and the work piece surface. The highly fail-safe system automatically adjusts to the height of the work piece and keeps an ideal distance, even in the case of bumpy work pieces.
|
Desludging system
The automatic, SPS controlled, abrasive desludging system uses a high-performance pump to take in abrasive water from the Waterjet Systems. Water and abrasive are separated and a second high-performance pump reintroduces the water into the jet catcher via two rinsing heads. The abrasive can then either be disposed of in dry state or be recycled. This system helps you to save resources and to protect the environment!
|
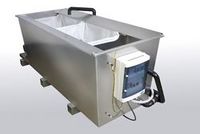 |
|
|